Le fasi di produzione
Un processo produttivo di matrice artigianale
Ogni nostro occhiale viene realizzato interamente all’interno del nostro stabilimento produttivo: dal concept, passando per tutte le fasi di produzione dei semilavorati, fino a packaging e controllo qualità.
La linea guida del nostro progetto è adattare l’artigianato all’industria, nel concept di artigianato fusion: nell’anno 2022 è ormai chiaro che le dinamiche globali di mercato e nazionali per quanto riguarda la scarsa protezione del vero Made in Italy, hanno portato all’esigenza di creare dei prodotti che possano unire rispetto e riconoscimento della qualità intrinseca dell’oggetto ad un processo produttivo che ne permetta di poterli immettere sul mercato ad un prezzo accessibile.
Con questo obiettivo siamo riusciti a sviluppare un processo produttivo di matrice artigianale che abbina e ottimizza fasi e processi di carattere più automatizzato, seppure sempre sotto la guida vigile e accurata dell’uomo.
Oltretutto ci dà la possibilità e la flessibilità di creare piccole collezioni su misura, non essendo vincolati ai numeri che impongono forzatamente l’impiego di grandi macchinari. Nel seguito illustriamo le fasi principali di realizzazione di un nostro occhiale, con riferimento alla strumentazione realmente presente nel nostro laboratorio.
Ideazione
La nostra azienda era già dotata al suo interno di un ufficio grafico, per tutte le personalizzazioni che realizziamo sui vari articoli prodotti e commercializzati dal gruppo LLEXAN ITALIA. Con l’avvento del progetto E4Y, abbiamo svolto dei corsi di progettazione CAD 2D/3D, mirati al settore ottico, in maniera tale da acquisire le competenze necessarie per poter sviluppare autonomamente i nostri e i vostri disegni/idee.
Una nostra prima versione 3D ante produzione di ogni modello poi fisicamente realizzato costituisce la base del configuratore, che potete trovare nella sezione dedicata.
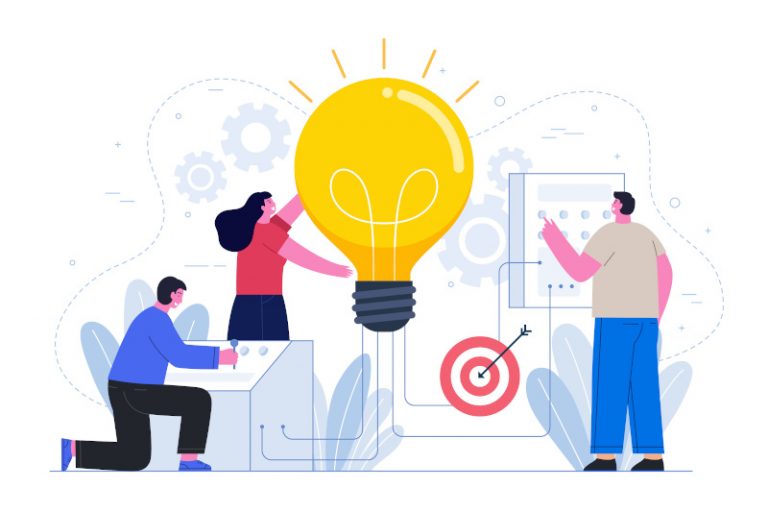
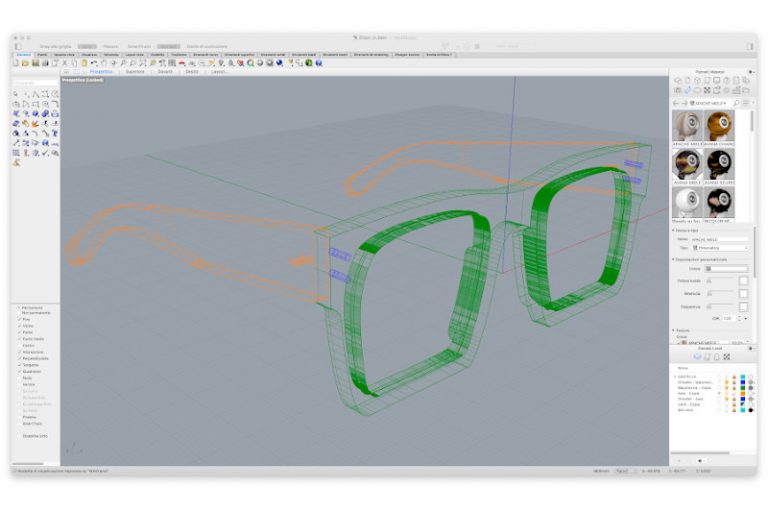
Prototipazione
Una volta realizzato il disegno 2D/3D dell’occhiale, si passa a virtualizzarne la fresatura, attraverso un software dedicato e che trova ampio utilizzo nel settore della falegnameria, configurato in maniera da rispecchiare le caratteristiche e le frese poi realmente impiegate.
Grazie a questa possibilità, una volta indicate la misura della tavoletta di acetato e del modello da tagliare, si possono simulare tutte le fasi di taglio, in modo tale da ottimizzare i tempi di esecuzione, minimizzare gli sfridi e non rischiare di compromettere alcuna tavoletta fisica. Validato il processo viene creato il file che il macchinario CNC eseguirà pedissequamente.
Materiali
Le nostre collezioni sono composte interamente da lastre di acetato, provenienti dai più noti fornitori italiani del settore. L’acetato di cellulosa è un materiale di origine naturale composto principalmente da cellulosa ricavata dalla pianta del cotone e da fibre di legno da cui, dopo uno speciale trattamento, deriva l’acetato.
Viene fornito generalmente in lastre di grandi dimensioni, dalle quali ricaviamo delle tavolette di dimensione indicativa 180x70mm per i frontali, che verranno successivamente fresate da un CNC per ricavare il pezzo principale dell’occhiale. Impieghiamo prevalentemente spessore 8mm per i frontali e spessore 4mm per quanto riguarda le aste.
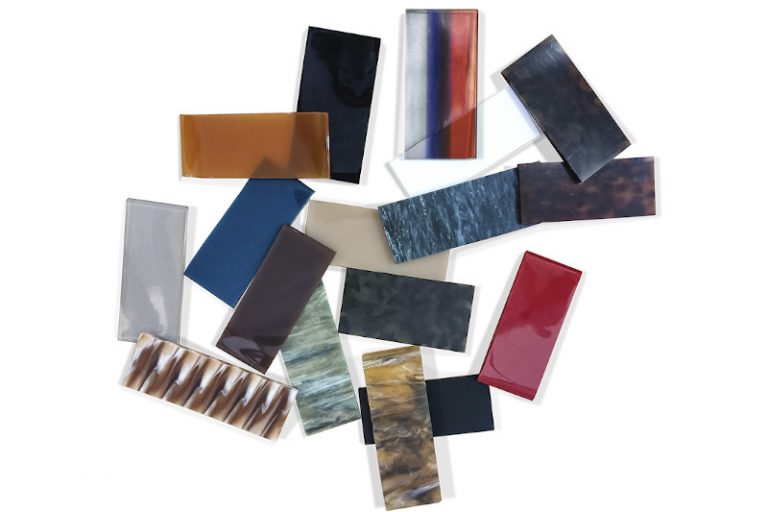
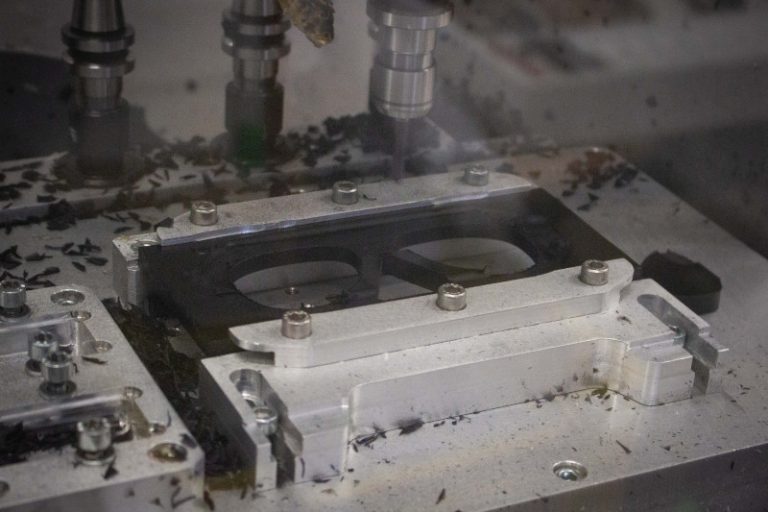
Fresatura
Una macchina a controllo numerico (CNC) mette in atto quanto simulato al computer, ottenendo la sagomatura di frontale e aste attraverso tre passaggi separati. Un operatore fissa le tavolette sul piano di lavoro e carica il lavoro da eseguire tramite un software dedicato.
Sei frese dalle forme e dimensioni differenti si adoperano per realizzare il lavoro: una sgrosserà la superficie, una più ovalizzata traccerà il naso, una piccolissima forerà i buchi per le viti, un’altra traccerà invece sedi delle cerniere e la superficie esterna del pezzo; una diversa ancora, ad esempio, scaverà i canali per le lenti.
Burattatura
Frontali e aste ancora non assemblati attraversano ora un lungo processo naturale di lenta ed incessante, seppur delicata, erosione ad opera del buratto. Si tratta di un macchinario motorizzato composto da quattro differenti vasche chiuse, che girano alla stessa fase e sempre nel medesimo senso, ma con una sola quanto sostanziale differenza: vengono riempite ognuna con un particolare tipo di sagoma ed essenza di legno miscelate ad una pasta appropriata, per conferire ad ogni passaggio uno specifico effetto. Ogni fase della burattatura dura dalle 10 alle 12 ore. La sgrossatura e levigatura, come fa presagire il nome, eliminano le eventuali piccole imperfezioni della fresatura e arrotondano le estremità dell’acetato, aiutando anche la calzabilità della montatura. Sono prevalentemente di carattere funzionale. Un occhiale opaco può dire di aver completato il suo ciclo, dopo aver sostenuto questi due passaggi. Nel caso invece di montature lucide, le restanti vasche di lucidatura e brillantatura, conferiscono al materiale quell’effetto per l’appunto lucido e specchiato, tipico della maggior parte dei prodotti in commercio.
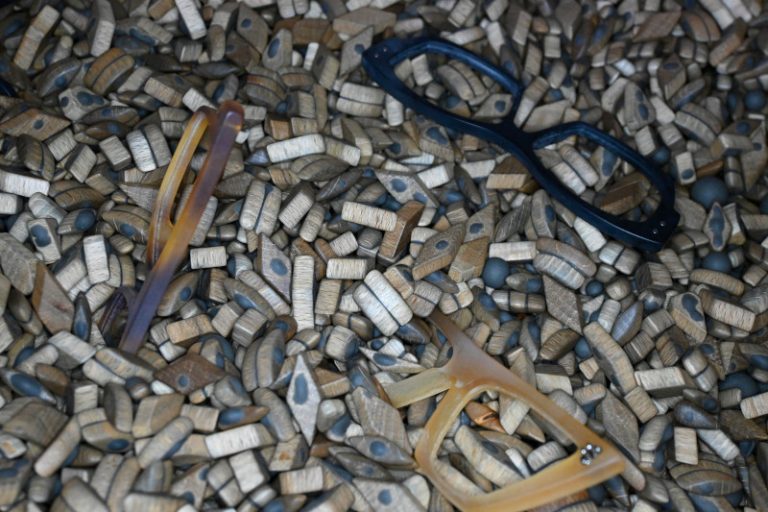
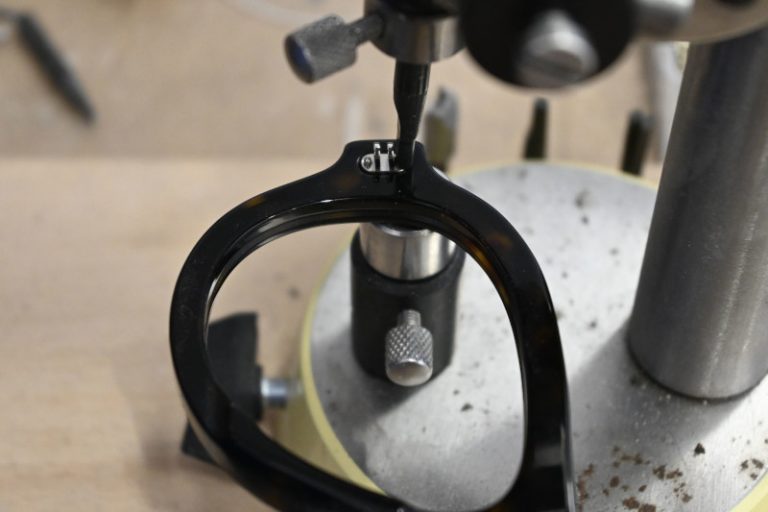
Finissaggio
L’ultima fase produttiva è quella del finissaggio, in cui spicca maggiormente la manualità del processo. Gli addetti ora devono tagliare le lenti, siano da sole o di presentazione, garantendo sempre un livello di controllo della qualità del prodotto finito consono alla storia del Made in Italy. Viene poi aggiunta la personalizzazione delle aste mediante incisioni a laser; laser che può essere coinvolto anche in alcuni lavori di personalizzazione della montatura. Al termine dell’intero processo avviene la fase di registratura. Tutti i componenti delle montature per occhiali da vista e occhiali da sole, siano acetati o lenti, vengono controllati singolarmente. Si appongono e si fissano le cerniere mediante dei torchietti su frontale e aste, poi si assemblano. Il pezzo viene poi meniscato per conferirgli la naturale e fisiologica curvatura. Durante questa fase viene garantita anche la calzata degli occhiali. Un passaggio finale a mano in una ruota con tessuto serve per ridonare un ultimo tocco di lucidità e brillantezza eventualmente sbiadito nei passaggi successivi alla burattatura. In ultimo, ogni singolo pezzo viene confezionato nel proprio packaging.