Production steps
An artisanal manufacturing process
Each of our glasses is made entirely in our own production facility: from the concept, through all the production phases of the semi-finished products, to packaging and quality control.
The guiding principle of our project is to adapt craftsmanship to industry with the concept of “handicraft fusion”. Nowadays, global market and national dynamics regarding the lack of Made in Italy protection have led to the creation of products that combine respect and recognition of its intrinsic quality with a production process that allows them to be placed on the market at an affordable price.
With this in mind, we have succeeded in developing a handcrafted production process that combines and optimises phases and processes of a more automated nature, always under the watchful and careful guidance of man.
In addition, it gives us the possibility and flexibility to create small, customised collections, not being bound by numbers forcing the use of large machinery. Hereby, we illustrate the main stages in the production of one glass, with reference to the equipment present in our workshop.
Concept
Our company was already equipped with an in-house graphics department for all the customisation on the various articles produced and commercialised by LLEXAN ITALIA’s group. With the E4Y project, we held 2D/3D CAD design courses focused on the optical sector to acquire the necessary skills and be able to develop designs/ideas independently.
Our first 3D pre-production version of each model forms the basis of the configurator, which you can find in the dedicated section.
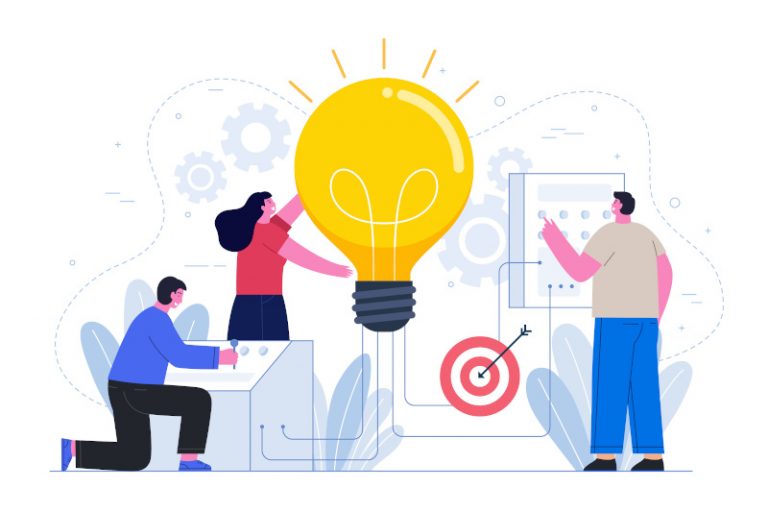
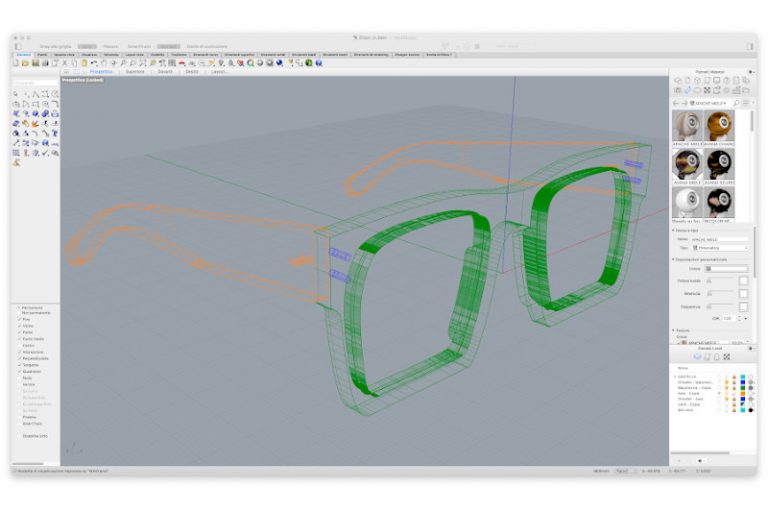
Prototype
Once the 2D/3D drawing of the spectacle has been realised, we move on to virtualise the milling process, through a dedicated software widely employed in the carpentry sector, configured to reflect the characteristics and milling cutters actually used.
Thanks to this possibility, once the dimensions of the acetate slab and the model have been indicated, all the cutting phases can be simulated to optimise execution times, minimise waste and not compromising any physical sheet. Once the process is validated, the file is created and the CNC machine will execute slavishly the work.
Materials
Our collections are composed entirely of acetate slabs, sourced from the best-known Italian suppliers in the industry. Cellulose acetate is a material of natural origin composed mainly of cellulose obtained from the cotton plant and wood fibres from which acetate is derived, after a special treatment.
It is generally supplied in large sheets, then we cut smaller parts of approximately 180x70mm for the fronts, then milled by a CNC to obtain the main piece of eyewear. We mainly use 8mm thickness for the fronts and 4mm thickness for the temples.
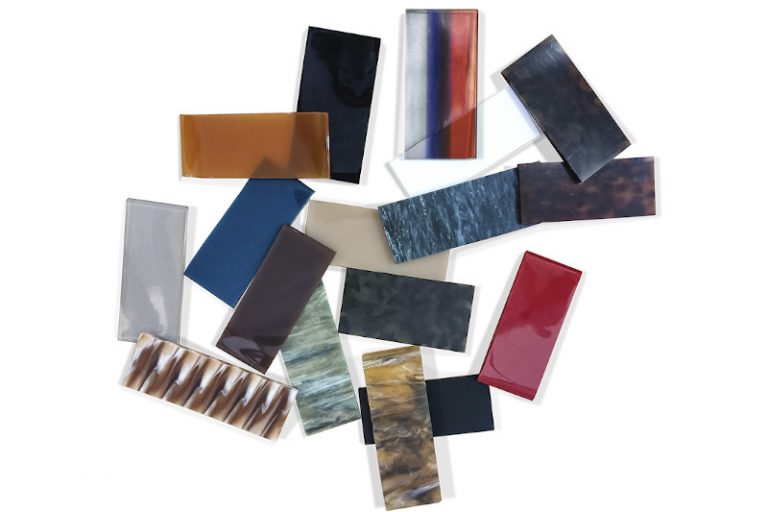
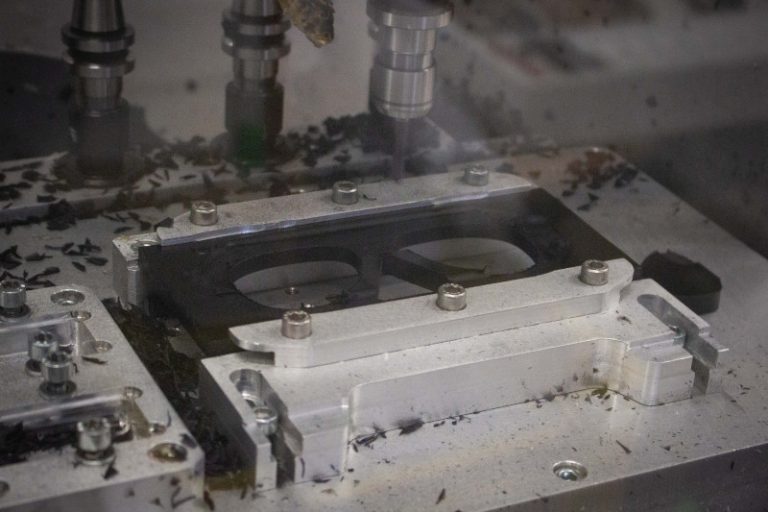
Milling process
A numerical control machine (CNC) implements the simulation on the computer, shaping the front and temples through three separate steps. An operator fixes the slab on the worktable and loads the software.
Six milling cutters of different shapes and sizes are used to carry out the work: one will rough the surface, a more ovalized one will trace the nose, a very small one will drill the holes for the screws, another will trace the hinge seats and the outer surface; a different one will dig the bevels for the lenses, for example.
Tumbling
Now, unassembled fronts and temples go through a long natural process of slow, incessant but gentle erosion by the tumbler. This is a motorised machine consisting of four different closed tanks, which rotate at the same pace and in the same direction. There is only one substantial difference: they are each filled with a particular type of shape and wood essence mixed with an appropriate paste to give a specific effect. Each tumbling stage lasts between 10 and 12 hours. Roughing and sanding remove any small imperfections from the milling and round off the edges of the acetate, helping the fit of the frame. They are mainly functional. A matt spectacle has completed its cycle after these two steps. On the other hand, shiny frames have left the remaining polishing and shining tanks that give the material the brightness, mirrored effect, typical of most products on the market.
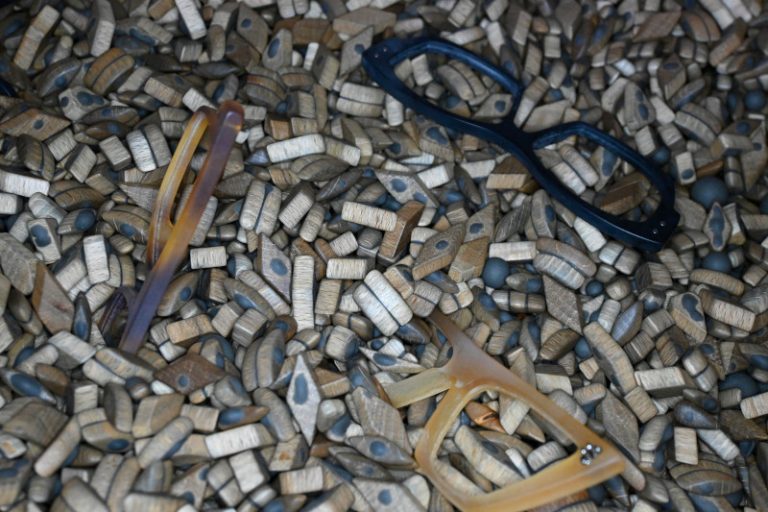
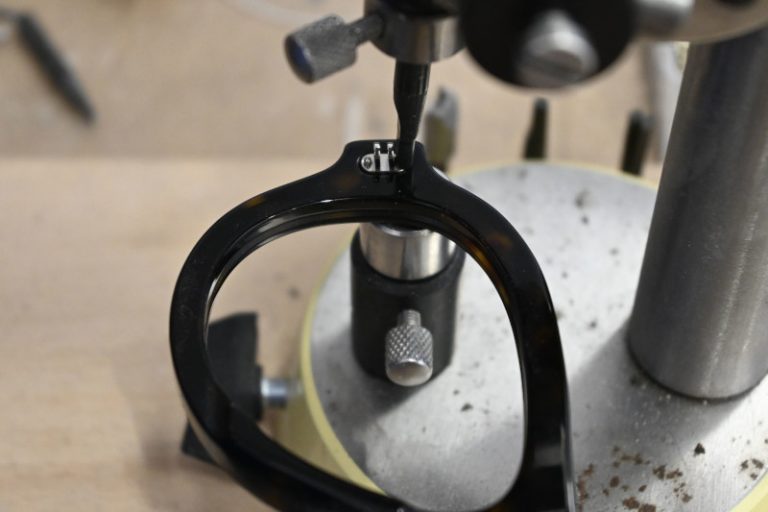
Finishing
The last stage of production is the finishing, where the manual skill of the process stands out the most. Now, the operators have to cut the lenses, whether sunglasses or presentation lenses, always guaranteeing a level of Made in Italy quality control of the finished product. After that, it’s time to customize the temples with a laser engraving, that can also be involved in some customisation work on the frame. At the end of the entire process, the registration phase takes place. All frame components for prescription glasses and sunglasses, whether acetates or lenses, are individually checked. Hinges are affixed and fixed by presses on the front and temples, then assembled. Then, the product is bended to give it a natural, physiological curvature. During this phase, the fit of the glasses is also ensured. A final handcrafted passage in a rotating wheel restores a final touch of gloss and shine that may have faded in the tumbling process. Finally, each individual piece is packed in its own packaging.