Riessere Unici
A recursively infinite process
The topic of recycling, linked to environmental protection, is increasingly relevant: everyone should feel obliged to contribute and care more of the planet. Companies are no exception and we contribute in this way.
The first times the CNC machine was at work in our workshop, we realised that the weight of a milled front is on average between 15 and 20 grams, while an intact slab weights around 100 grams; this means that 70% / 80% is discarded and becomes unusable acetate scraps that are not commonly recycled. After collecting the first sacks of production waste, we wondered if something could be done to recover what is ultimately material from which a frame is made, without any imperfections whatsoever. The idea was to reconstruct a new acetate slab from the waste of others. But how to do it?
After a few months of research, we managed to find a machine that further shreds the acetate waste to create micro pellets all same size. At this point, all we had to do was find a way to recreate a slab from those acetate balls. Further investigation led us to a craftsman who makes ovens essentially for making ceramic objects. Then, we tried to have him commission an ad-hoc oven for trying to melt the acetate scraps into solid shapes. The first tests were not encouraging, but we did not give up and we are proud to present our project related to recycling and environmental protection as you can see from the photos:
Riessere unici
Ri- (=again) - because we bring to life cellulose acetate production waste that would find its natural destination in industrial composting;
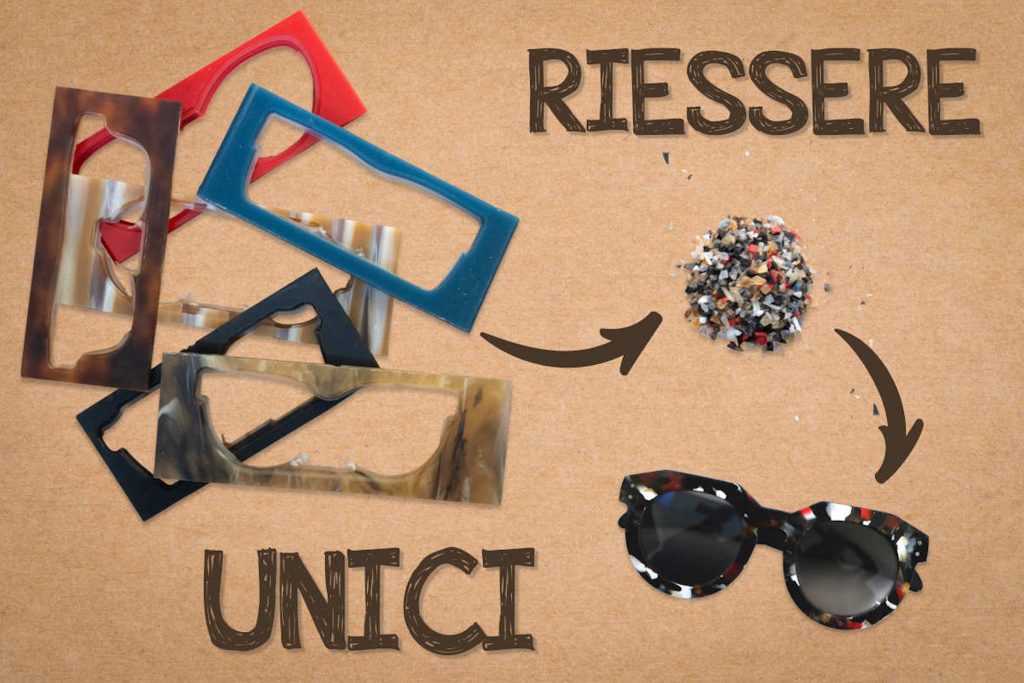
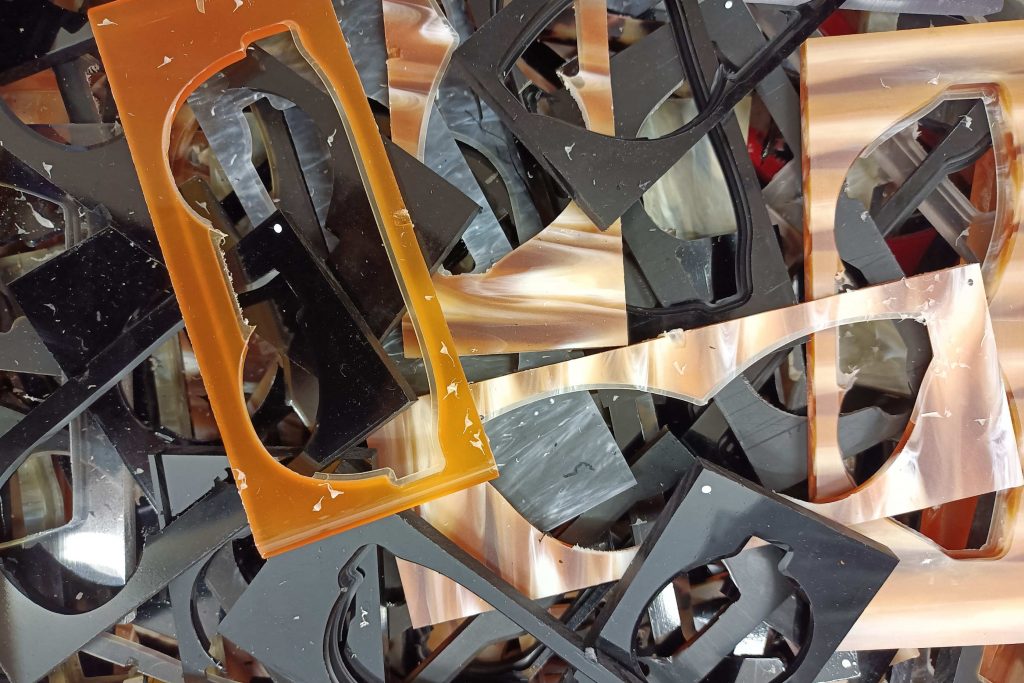
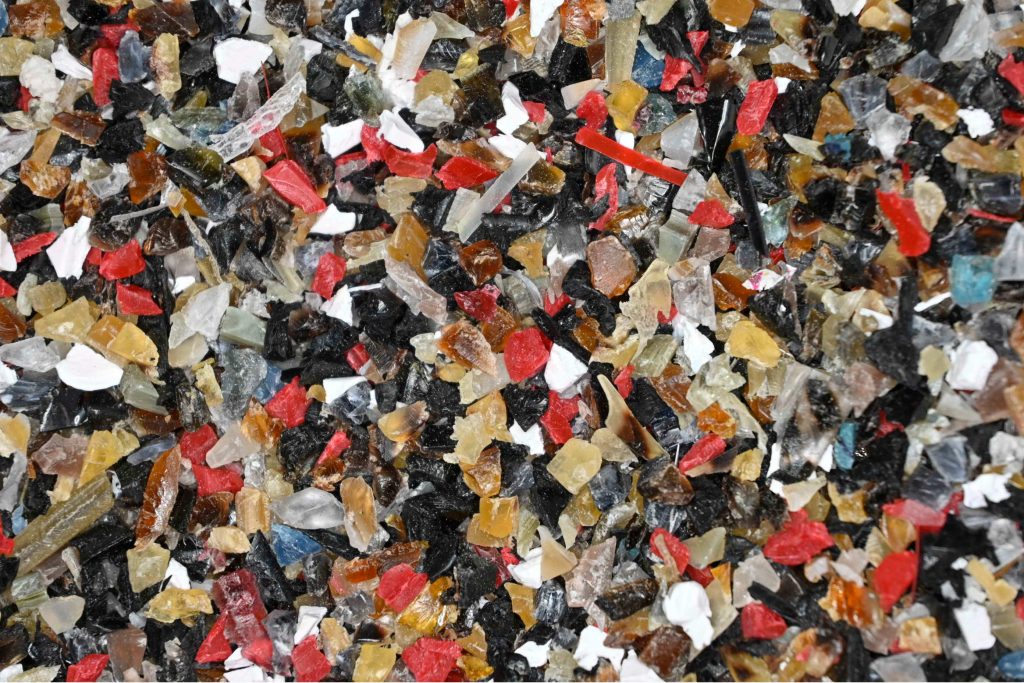
This process can be applied to any object that can be melted in an oven. By making suitable moulds, we can make accessories ranging from trays to vases... the limit is the imagination.
Clearly, the recycling process is recursively infinite, as shavings will be made from each recycled slab that will re-initiate the recovery and melting process.
Hereby, we will make available the unique re-moulding slabs currently available or ask through the usual contact channels.